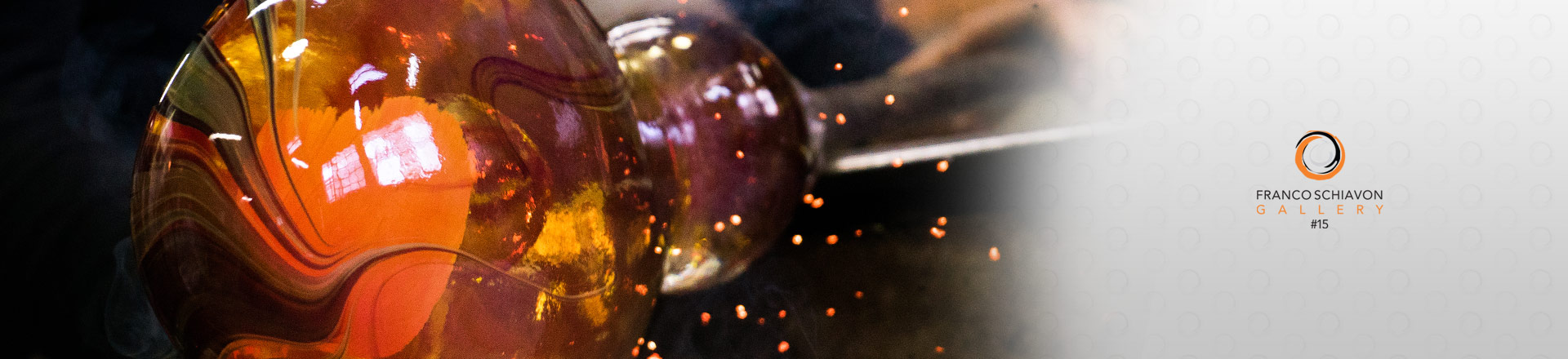
Glassworking techniques, the Magic of Glass
Glass is a solid material made from a blend of silica sand, soda, lime, and potassium. These components are melted together in a furnace at 1,500°C (2,700°F) to create a malleable substance. The glassmaker gathers the molten glass using a blowpipe and shapes it with traditional tools such as tongs, shears, and wooden paddles.
“Glassblowing” refers to the technique artisans use to shape the material by blowing air through the pipe.
The stunning appearance and vibrant colors of Murano glass are achieved by adding gold or silver leaf and mixing minerals into the molten glass—zinc for white, cobalt for blue, manganese for purple, and so on.
Once the piece is formed, it is placed in a cooling oven called an annealing kiln, which gradually lowers the temperature to prevent thermal shock and breakage.
ALEXANDRITE
Alexandrite Glass is renowned for its striking color-changing effects. It appears lilac or pink under natural sunlight or warm artificial light, while shifting to smoky blue under fluorescent or white light. This unique color play is due to its chemical composition, which includes neodymium oxide and selenium.
Glass containing neodymium has been produced in various countries, but some of the finest examples come from Murano, where artists like Dino and Loredano Rosin have achieved exceptional results.
AVVENTURINA GLASS
Avventurina glass is a translucent material enriched with sparkling metallic oxides, giving it a resemblance to the natural quartz of the same name. It is created by adding copper and chromium oxides to the molten glass, allowing for a slow crystallization process that produces a fine, shimmering dust effect in warm brown-green tones. The name derives from ventura, referencing both the chance discovery of this technique in the 17th century and the challenging nature of its production—considered a true test of skill even for master glassmakers.
CHALCEDONY GLASS
Calcedonia glass is crafted by blending different metal oxides to mimic natural stones such as chalcedony, malachite, and agate. Copper, iron, nickel, and silver oxides are commonly used, resulting in striking iridescent veining and shifting colors that range from blue and violet to brown and green. This technique is highly complex, with unpredictable results depending on minute variations in chemical composition and working temperature. First developed in Venice in the late 15th century, it was lost for centuries before being rediscovered in the 19th century.
CANNA – GLASS RODS
Canna glass is made by assembling round or flat, multicolored glass rods, which are then fused and blown into shape. Each rod is individually crafted by stretching molten glass into fine threads. These can be solid-colored or feature intricate internal designs, such as flowers, spirals, or stripes. This technique has been integral to Murano glassmaking since its origins, reaching its peak between the 16th and 17th centuries when filigrana and zanfirico glass became symbols of luxury and aristocracy. Today, it remains highly valued for both decorative objects, such as glasses and plates, and unique, prestigious artworks. Among the most notable contemporary masters are Maurizio Alfier, Studio Salvadore, and Luca Vidal.
VENETIAN CRYSTAL
Crystal glass, originally perfected between Bohemia and France in the 17th century, is known for its exceptional clarity. In Venice, however, cristallo refers to a pure, flawless glass. Venetian crystal was the first truly colorless glass, invented in 1450 by master glassmaker Angelo Barovier, who achieved its transparency by decolorizing the mixture with manganese or other refining agents. Unlike lead crystal, Venetian crystal is a delicate, sodium-based glass, ideal for intricate hand engraving.
FILIGREE OR RETICELLO
One of the oldest glassmaking techniques, dating back to the 16th century, filigrana is created by arranging transparent glass rods with a colored core on a heated metal plate until they reach the melting point. The softened rods are then rolled onto a cylindrical form, adhering to its surface. The technique is called reticello when the colored cores intersect, forming a grid pattern with tiny air bubbles inside each diamond-shaped cell. A retorti or retortoli glass features twisted, spiral-like filaments. Widely considered the most iconic Murano glass technique, filigrana is a hallmark of Venetian craftsmanship. Beyond traditional Tipetto goblets, this technique is used by master glassmakers such as Luca Vidal, Afro Celotto, and Stefano Dalla Valentina to create large-scale works of art.
GOLD AND SILVER LEAF
A paper-thin sheet of 24-karat gold, typically measuring 8×8 cm (3.15×3.15 in), is applied to molten glass at the early stages of shaping. The gold leaf can then be encased in a transparent glass layer. When blown, the delicate gold sheet fractures into a shimmering effect known as pulviscolo aureo (gold dust). Since the 19th century, silver leaf has also been used, but it must be encased in another glass layer to prevent oxidation and discoloration.
INCALMO
A traditional Venetian technique that involves seamlessly joining two or more hot glass elements of different colors to create a single form. This process requires exceptional skill from the master glassmaker. A famous example is the double-incalmo vases presented by Venini at the 1962 Venice Biennale, including the Cappello del Doge (Doge’s Hat) designed by Thomas Stern.
COLD ENGRAVING
A decorative finishing technique performed on the glass surface using a grinding wheel. The engraving can vary in depth: broad and flat etching is called battitura or martellata (battuto), while a softer grinding technique that creates a frosted effect is known as velato. This surface treatment has been used by some of the greatest contemporary artists and Murano masters, including Carlo Scarpa, Alfredo Barbini, Lino Tagliapietra, Davide Salvadore, Luca Vidal, and Yasuhiko Tsuchida.
INCAMICIATO – LAYERED GLASS
A technique similar to sommerso glass but typically thinner, incamiciato consists of two overlapping layers of glass. Today, it is particularly popular in the production of modern chandeliers.
LAMPWORKING
Although lampworking shares certain techniques with other hot glass methods, it stands out for its affordability and versatility in crafting small objects such as miniature sculptures, animals, and beads. The focused flame of the burner allows for exceptional precision, giving the artist great creative freedom. This technique fosters a close connection between the artisan and the flame, encouraging artistic expression and the development of a personal style. On one hand, lampworking allows for spontaneous shaping; on the other, it enables adjustments and refinements that are impossible with other thermal processes. Notable artists in this field include Dario Frare and Lucio Bubacco.
MOSAIC
The mosaic technique, also known as the tesserae method, involves assembling small, colored glass pieces—called smalti or paste—which are cut from blown glass sheets. These tesserae are then fused together and gathered onto a blowing pipe to be shaped into the desired form, typically a vase. One of Murano’s most ancient and fascinating techniques, mosaic glass is renowned today thanks to artists such as Carlo Scarpa and Maurizio Alfier.
MURRINA OR MILLEFIORI
Dating back to ancient times, this technique was originally developed by Syrian, Egyptian, and Roman artisans. After falling into obscurity, it was revived in the mid-19th century and reached its peak in the early 20th century with masterpieces from the Barovier family. The process begins with the creation of a bundle of multicolored glass rods, arranged to form floral or geometric patterns. The bundle is fused together and then sliced into small cross-sectioned discs. These discs are arranged on a metal plate to form the desired pattern, reheated, and fused onto a glass surface attached to a blowpipe.
OPALINE GLASS
Opaline glass can take on various shades depending on the type and amount of substances added, such as sodium phosphate or talc oxide. Its color spectrum ranges from white to black, including hues of gray, pink, green, lavender, golden yellow, light blue, and deep blue. The classic milky-white opaline glass made in Murano was originally produced using significant amounts of arsenic oxides, which have since been banned due to their toxicity during production. As a result, historical opaline pieces with this composition are now unique and impossible to replicate, making them particularly rare and valuable.
SCAVO
Named after its distinctive finish, which mimics ancient Roman glass unearthed from archaeological excavations, scavo glass was introduced by Cenedese in the 1940s and later refined by other Murano artisans. It is characterized by a rough, matte surface—predominantly gray, with scattered bursts of color. This aged, uneven appearance is achieved through a chemical reaction involving salts and mineral oxides applied to the glass surface during the final stage of production.
SOMMERSO – SUBMERGED GLASS
Famous for its purity and vibrancy of colors, sommerso glass creates striking effects of layering and tridimensionality. This effect is achieved by immersing the object in molten glass of different colors, preserving the depth and brightness of each hue. The technique requires exceptional skill in temperature control and the glassmaker’s craftsmanship. Introduced in the 1930s, it reached its peak popularity in design objects of the 1950s and 60s. Today, it remains one of the most appreciated and sought-after techniques internationally.
RUBY GLASS
Ruby glass is one of the most distinctive colors in the Murano glassmaking tradition. The minerals used in its composition would typically produce a completely different hue if not for the addition of pure gold and a specific acid, which triggers a precise chemical reaction. The result is an intensely vibrant, homogeneous pink—transparent yet deeply saturated.
ZANFIRICO
A technique similar to murrina, zanfirico is created by bundling together glass rods of various colors, heating them until they fuse, and then pulling and twisting the bundle into a delicate spiral pattern. The modern term zanfirico is used in Venetian glassmaking to describe this variation of retorti (twisted filigree).